When I started this site, my hope was that some ex-employee would find me and tell me their story. I really lucked out when Steve found me. I knew well of his many exploits over decades at the coke plant and he was eager to tell me about the other 99%.
Apparently you found my video!
I did find your tape and I would never keep what is not rightfully mine. I would gladly return it…
No, I do not want the tape – that’s not what I meant. I was so surprised to see it, and all the other references to my days at Interlake and Acme Steel. My wife (who also worked there in Human Resources and authored those job transfers you posted) and I knew Doug Podgorny – myself more than she – but he will remember both of us. We are now retired and live in Georgia. Her correspondence (with her handwritten notes on it) are what first drew my closer scrutiny to your website. I recognized her handwriting immediately.
How did you get started at Interlake?
In 1967 I started in the furnace plant and later transferred to coke – at the bottom rung. I went to Coyne night school in downtown Chicago for electrical and got a position at the coke plant as motor inspector in 1970. I got bored and applied for an instrument technician position and got the job.
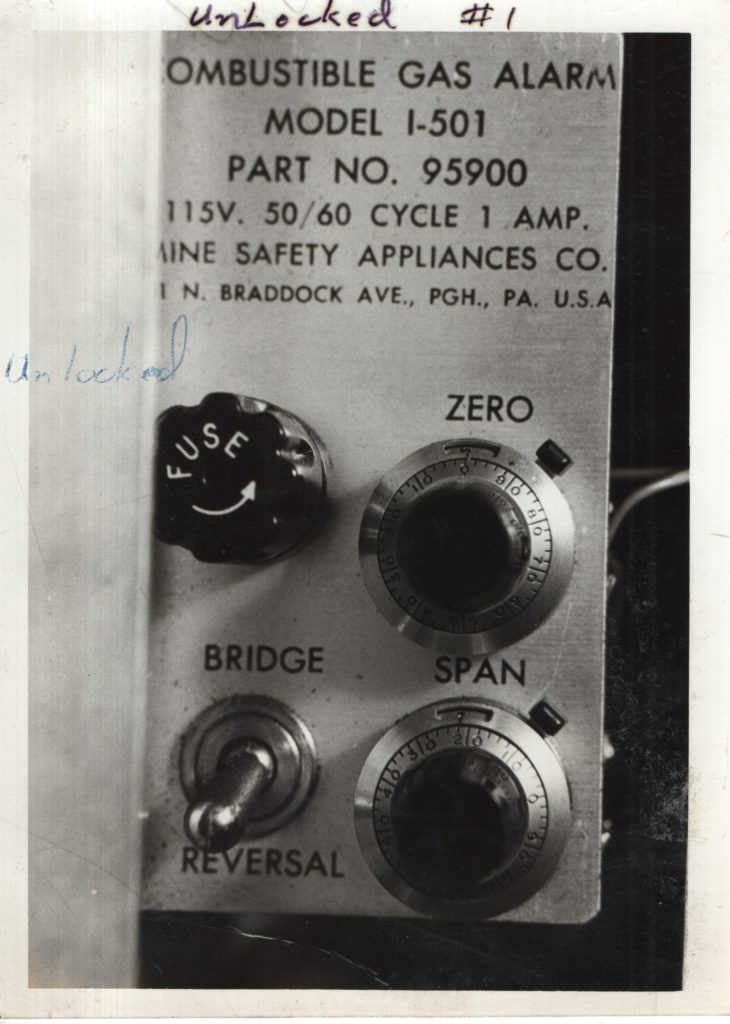
I was responsible for all the plant measurement and control systems – the ‘Instrumentation”. To heat the battery and control the off gases in the collector main…there was a lot going on. I found out early on that anytime there was a process anomaly, indicated by a change in a process variable away from normal, the Instrument group would be called to check the measuring/control devices. Almost always there was not a problem with the instrumentation but a process related issue that was being correctly recorded. I knew the solution was to become an expert in measurement, control, and process. So I studied and learned the inner workings of coke making and by-products operations. I enjoyed the research and found it fascinating! That’s how my knowledge of the plant evolved and how I trained my group. The boredom to conduct a 30 year career without something new and fresh would have killed me. At the same time I was working for myself and personal fulfillment!
Did you have any involvement in the coke industry after Acme closed in 2001?
After Acme I moved just down 130th to Lafarge Steel. I later worked at Arcelor Mittal in Indiana Harbor then AM Bayou Steel in Louisiana. I ended my career at Arcelor Mittal Burns Harbor coke plant in 2012 and retired in February 2020. It was larger than Acme – the plant has two 6M batteries with 82 ovens each. Battery #1 was built by Wilputte in 1969 and was rebuilt in 1984. Battery #2 was built by Koppers in 1972 and rebuilt in 1992.
I had a dream recently that the plant was still running and I was trying to make contact with anyone I could reach to pass on things I thought others should know. When I woke up I realized it was shut down! I actually googled ‘Podgorny’ and your site popped up. We used to be buds.
I found a report of an electrical accident you might be aware of.
My partner at the time was the supervisor for the job. He handled the electrical and I the instrumentation. I was qualified to perform either but he was running that job that day. They needed to clean the high voltage sockets for the main breaker.

What they failed to realize is that the main breakers are bottom fed. Most of the time – but not always – breakers, switches and gear are top fed. These breakers were bottom fed, and directly connected to the 12kv/2.4kv transformer. When the main was closed, the power was fed up and energized the bus. The load breakers were then being top fed. When testing, they checked the top side only.
The electrical tech made contact with a metal scraper and a huge arc flash engulfed him. He survived but was never the same. He became very religious. Something about the white light!
Can you give me some background on the venturi port inspection tape?
In the battery, you have a heating wall and then an oven chamber then another heating wall and another oven chamber. This repeats for 50 ovens and 51 heating walls. There are 29 flues per heating wall… 51*29=1479 flues per battery. You check four flues per wall to derive a battery average. But you also need to check every flue for any anomalies. That’s the purpose of a complete crosswalk. From that we derived averages for zones and the entire battery, and from this we adjust gas flow to increase or decrease the overall temperature.

Of the 1,479 flues each needs a gas and air supply. There is an optimum fuel to air ratio. – the flues don’t get the same amount of gas or air. The outer flues located near the ‘end of oven’ lose more heat by radiant losses. The inner flues – not so much. Also, the ovens are tapered from the pusher side to the coke side. So the coke side will require more fuel to transform the coal to coke (pyrolysis). Keep in mind the oven chamber does not contain air so there is no combustion taking place, only heating the coal in the absence of air and driving off the volatile matter (destructive distillation). The heating walls are completely isolated from the oven chamber. The gases liberated are drawn off to the collector main and pulled through the by-product plant.
The air that gets to the flues is metered by the venturi ports in the roof of the bus flue. The large concrete stacks control the amount of draft inducing the air flow. Ambient air is pulled into the bus flue and distributed via venturi ports to the regenerator which preheats the air. It is then delivered by internal brick channels to the flue where it mixes with the coke oven gas and is ignited by the hot refractory. You can remove a flue cap on top of the battery and see the combustion. The operators had concerns that not enough air was being delivered to the flue for complete combustion. There was no existing way to check and see if venturi ports we fully opened. They asked me to devise a method.
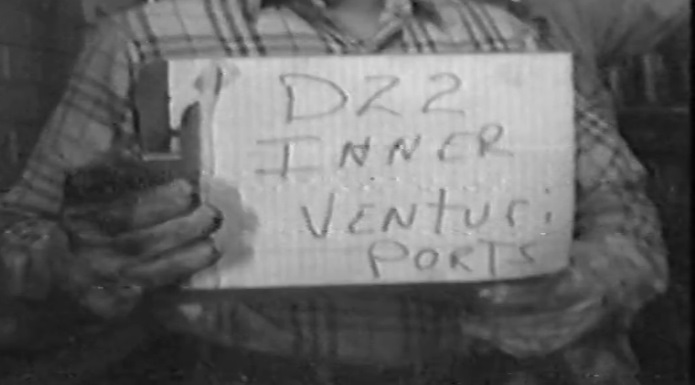
D22 and D23 were problem ovens to heat. Needed to check the combustion air circuit as other checks did not reveal problems. We were happy to see that there was not a lot of build up. Keep in mind that the battery reversed every 20 mins. When outers were burning the products of combustion rise in the flue and flow across the horizontal flue and are pulled down though the off zone regenerator and exit (reverse flow) through the venturi ports and bus flue out to the stack. So the venturis see both combustion air and flue gas when the zone is off. These flue gases are hot and transfer heat to the regenerator. The whole purpose of reversing is to re-heat the regenerators for the next cycle.
The camera was simply mounted to a metal plate I fabricated so it could slide on the bottom of the bus flue and look up. It was connected to a number of extension rods that could be screwed together as space was limited. I used Kaowool to insulate. The camera was whatever was available at the time that I thought met the specs. Long before GoPro!
Besides the venturi port inspection, did you do any other work on temperature control of the battery?
When I started calculators were only on the horizon. To be a heater helper you needed the ability to add long columns of numbers. Heaters did hand graphs by connecting dots on graph paper. I automated the heating forms and graphs with Lotus 1-2-3 using macro programming and upgraded the pyrometers to those that had data collection. Before data collection, the heater would read the temp aloud and the helper would write it down. Once I set up a collection system they had to walk their routes in a specific order.
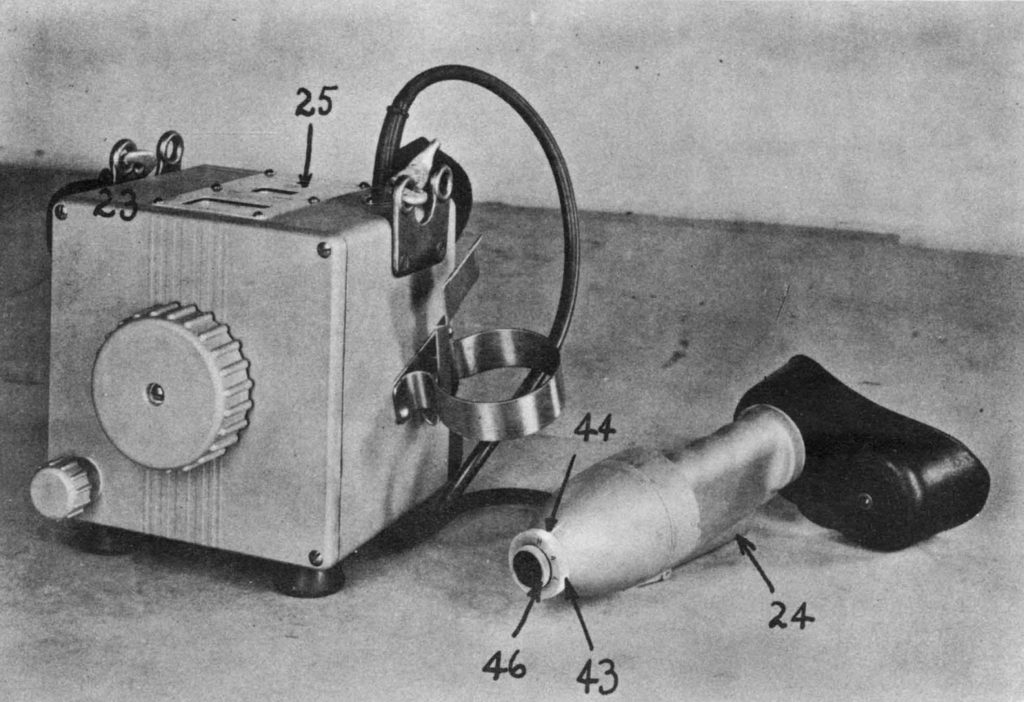
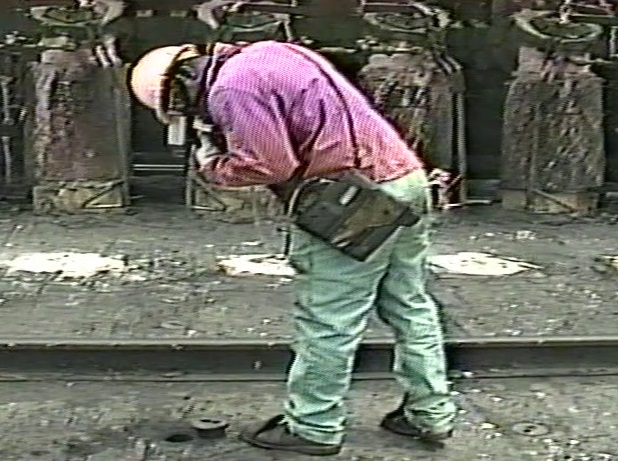
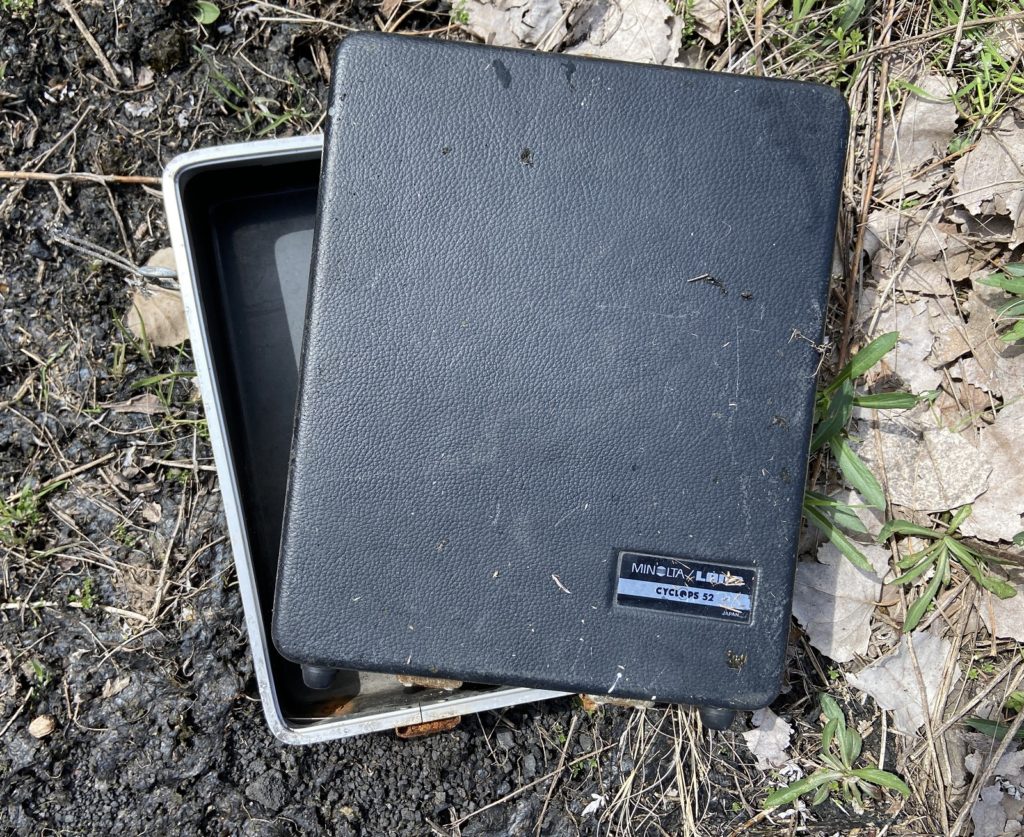
What type of pyrometers were they using initially?
Disappearing filament type. The heater would rotate a knob until the filament would disappear with hot flue in the background. Then they would read temperature on the drum. All heaters would see temperature a little differently (subjective error) that’s why we went digital once technology allowed. Later, we moved to the Land Cyclops 52.

I found quite a library of technical manuals in the electrical shop. Any knowledge of these?
I moved those catalogs under the stairs when they lost some degree of relevance. The office I shared was out front. My stuff was moved from when I built a new office down the road, in the old transformer vault (just west of the storeroom, since demolished).
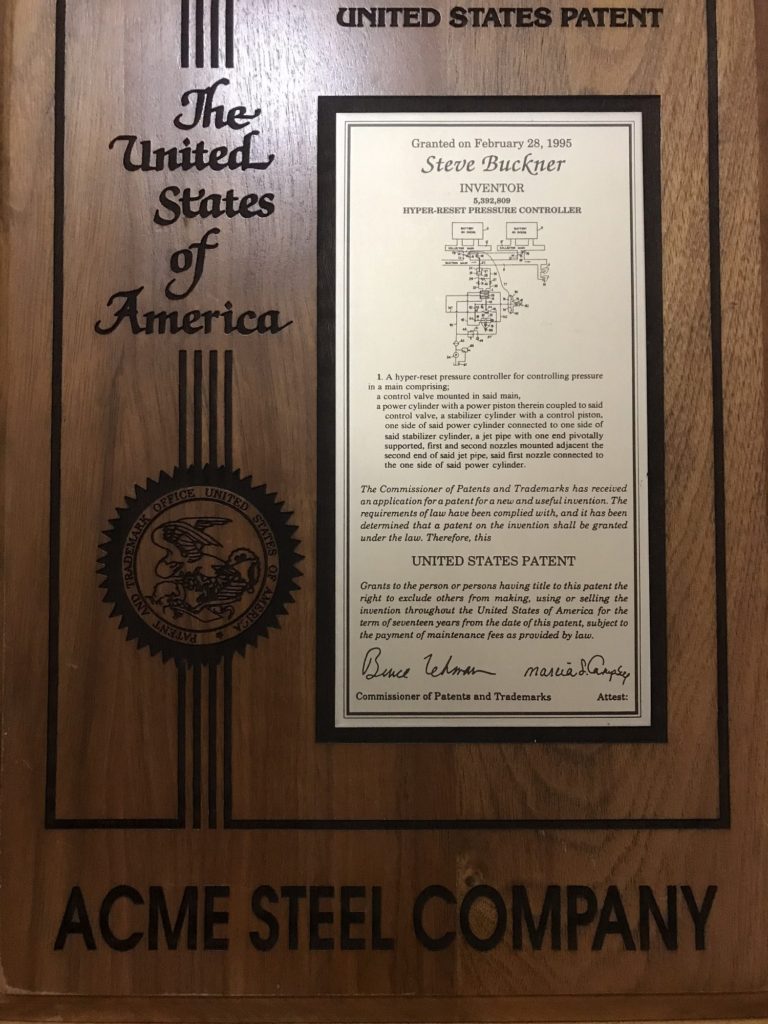
When I saw your name on the venturi port inspection tape, I did some research. One of the first things I came across was a patent. What can you tell me about that?
The plant used an Askania jet pipe hydraulic controller. This was technology from WWII, the Germans used for U-boat rudder controls. In 1955 (when the battery was built) it was the go-to hydraulic control used throughout coke plants: pressure control, stack control, turbine controls. Generally, the controller did it’s job – the patent only applied to the collector main process where speed of reaction and minimal reset time is critical.

So without your invention, charging would cause a pressure spike which would release emissions to the atmosphere?
Yes, it would break the fragile door seal knife edge to jamb. We also added ramping controls to the charging steam. The crossover valve is constantly modulating to hold pressure in the collector main at set point…eg 12mmwc (millimeters per water column) and the internal pressure on door seals directly correlates to collector main pressure. Most batteries (at the time of the patent) had a more modern approach. GPE/Askania tried to use my idea. That’s why we got the patent.

4 replies on “A Chat with Steve Buckner”
What a great interview with such a knowledgeable veteran of the industry. 50 years!!
Steve has been a huge resource. I am very lucky he found the site!
Well, the job postings that survived the test of time. On the other hand, I have really enjoyed reading Steve’s Coke Plant operations know-how. It is interesting and it captivates the knowledge he applied to make the Coke Plant a safe place to work. Thank you Steve and thank you Doug for doing this.
Thank you sir for taking the time to read and comment! I’m sure that you knew Steve well via your role in HR. There is no doubt his technical knowledge is second to none.