Digging through hundreds of pages of documentation I have pulled from the plant, I pretty quickly learned the names of some of the managers in the late 90s. One that came up again and again was Doug. After some sleuthing, I was able to contact him via email and ask him some of the nearly infinite list of questions I have. Look for more contributions from Doug in the near future.
How did you get started in the industry?
As I’m sure you’re aware, the site had been home to a coke plant since 1905. As a matter of fact, my maternal grandfather worked there for a bit in the late 30’s. Workers back then would show up at the gate very early and the lucky ones got picked to work for the day.
My coke plant career started in 1977, hired by Interlake (predated Acme) just out of college as a coal handling foreman. Through the years I was promoted as shift manager in all the operations areas (coal handling, by-products and the coke ovens). Later I took the job of Area manager for Pickling and Annealing over at the Riverdale facility (finishing plant at 135th and Perry). Just about two years prior to the shutdown I moved back to the coke plant as Coke Oven Area manager with the potential to move to division manager. Of course, we both know how that scenario ended.
Tell me a little bit about how coke gets used for steel making.
Making coke or the “carbonaceous residue left over after the chemical process of destructive distillation” was the primary fuel for the blast furnaces. Coke when properly made contained strength to support the other burdens of iron ore and limestone in the blast furnace. It was also porous enough to allow the hot gasses to permeate thru the burden as it reduced (melted the stone and ore) with a bonus of the carbon transfer to the “melt”. The blast furnace (previously at 107th and Burley, across the Calumet River) was charged from the top with alternating layers of stone, coke and iron ore. Hot gasses and air introduced from the bottom supported the chemical reaction as the materials melted. When there was sufficient molten material in the vessel it was tapped from the bottom. Slag which were the impurities in the ore and stone floated on top of the “tap” with molten iron on the bottom.
Can you explain more about how the coke plant functioned?
Acme Coke was a completely integrated operation containing a coal handling facility (rotary dumper for unloading coal rail cars and coal prep buildings), the coke ovens, a by products plant, powerhouse, and maintenance facilities to repair everything from conveyor systems to locomotives.
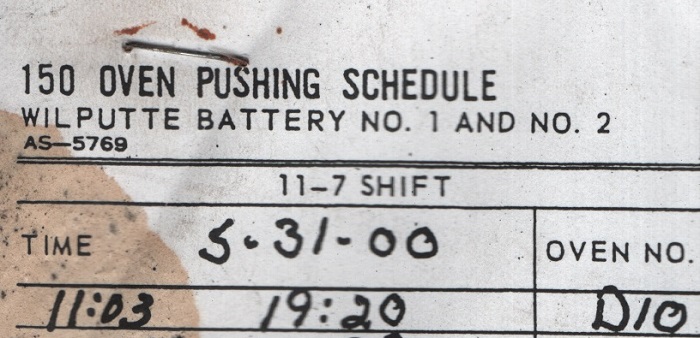
The north battery was #1 (A-section ovens 1-25, B1-25) with the south being #2 (C1-25 and D1-25). Both were Wilputte double divided under fire batteries. Wilputte devised this method theorizing that pushing and charging this way would minimize heat loss throughout the process of pushing coke and charging coal.
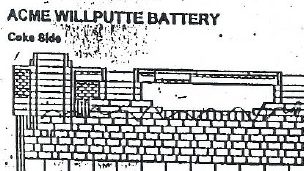
The ovens had two each of larry car, door machine, pusher and quench car. Mainly used one at a time although if circumstance dictated, we could use them simultaneously except for the quench car. No way to tell now but all machines ran on electricity with each machine having its own “hot rail” either hung along the battery or above it as in the case of the larry car. Each machine had a set of spring-loaded collector shoes kind of like arms with baseball gloves that would ride along with the machine and contact the rails. This setup allowed the machines to remain powered up over inconsistencies in elevation. The pusher had an air operated engine to use to retract the pusher stick (ram) in case power failed and the ram was in an oven. Larry car parts had to be crane lifted and assembled on the battery top. Each shift had one machine operator for each machine, two door cleaners one on each side, two lidmen to work topside and a spell man to “spell” or give breaks to the machine operators.
As oven manager, I can’t think of who to better explain how the batteries functioned. There is clearly much more than meets the eye.
- The basement level contained the gas underfire system. All piping containing the coke oven gas delivery system. Gas “main” delivered gas cleaned by the by products operation. The “main” gas was delivered to piping (gas header- one on each side of every oven) and the headers were like one of the gardening “seeping hoses” with gas delivered to each individual heating flue via metering pins. Don’t remember the exact number but each oven had at least 11 heating flues on each side. Air/gas flow was “reversed” on a regular basis to provide distributed gas on the burn cycle and hot air on the reverse to utilize the heat in the brick to burn off excess carbon in each flue. This was a closely monitored process. A bit of carbon was good (minimized friction, sealed any gaps in the brickwork) but too much was bad (blocked gas, increased oven pressure) and could grow to impact pushing, charging and even oven chamber integrity.
- Ground level was called the regenerator level – a design of channeled silicon fire bricks that utilized some of the heat in the brick to preheat the gas on the burn cycle and air on the decarb cycle. On the pusher side (west) there was the pusher pad which was nothing more than a concrete pad. On north (#1 pusher) and south (#2 pusher) the ends of the battery proper was an area where the pusher could be parked when not in use. The pusher ran on rails that ran parallel to the battery
- First level up was the bench level. The battery had a “deck” on the coke side and pusher side. The door machine ran on rails laid into the brickwork on the cokeside. The door cleaners worked on their respective sides from the bench. Patchers or the coke oven masonry crew would also work from the bench sealing door leakage and patching brickwork on the ends of an oven as required. When the door was removed on each side the cleaner would have to scrape carbon off the door jamb and then the gas channel in the door itself. We later added a Saturn Company Automatic door cleaner to each pusher and door machine. When adjusted properly it did a pretty good job. Coke side had a parking area on each side for door machine when not in use. The center area between both benches contained the turn foremen and heating managers office, employee lunch/break room and the area managers office. There was also an area just south of the area manager office where the patchers stored and prepared their material and tools.
- Next level up was “topside”. Two larry cars in total that ran on rails set into the brick. Parking areas on each end. Larry car had three charge hoppers to correspond to the three charging holes per oven. On top of the larry car was a gate opener that when positioned under one of the 4 separate coal bins above would be used to move a slide gate under each bin thereby gravity loading the prepared coal blend into each larry car hopper. On the battery top west side there were a series of posts which supported the “hot rails” that powered the larry car. Each oven charge hole (three per oven) had a cast metal casting set into the brickwork. Oven charge hole lids (cast metal disks) were removed to charge and replaced after by the lidman.
There were metal stairs at each end of the batteries leading down to basement and up to topside (stairs continued from the topside to the charging bins in the center area from the larry car loading area). There were also stairs on the pusher side between the batteries, from ground level to the bench level, the up to topside inside the battery.
As a by-product plant, Acme recycled oven emissions to then fuel the ovens. How did that work?
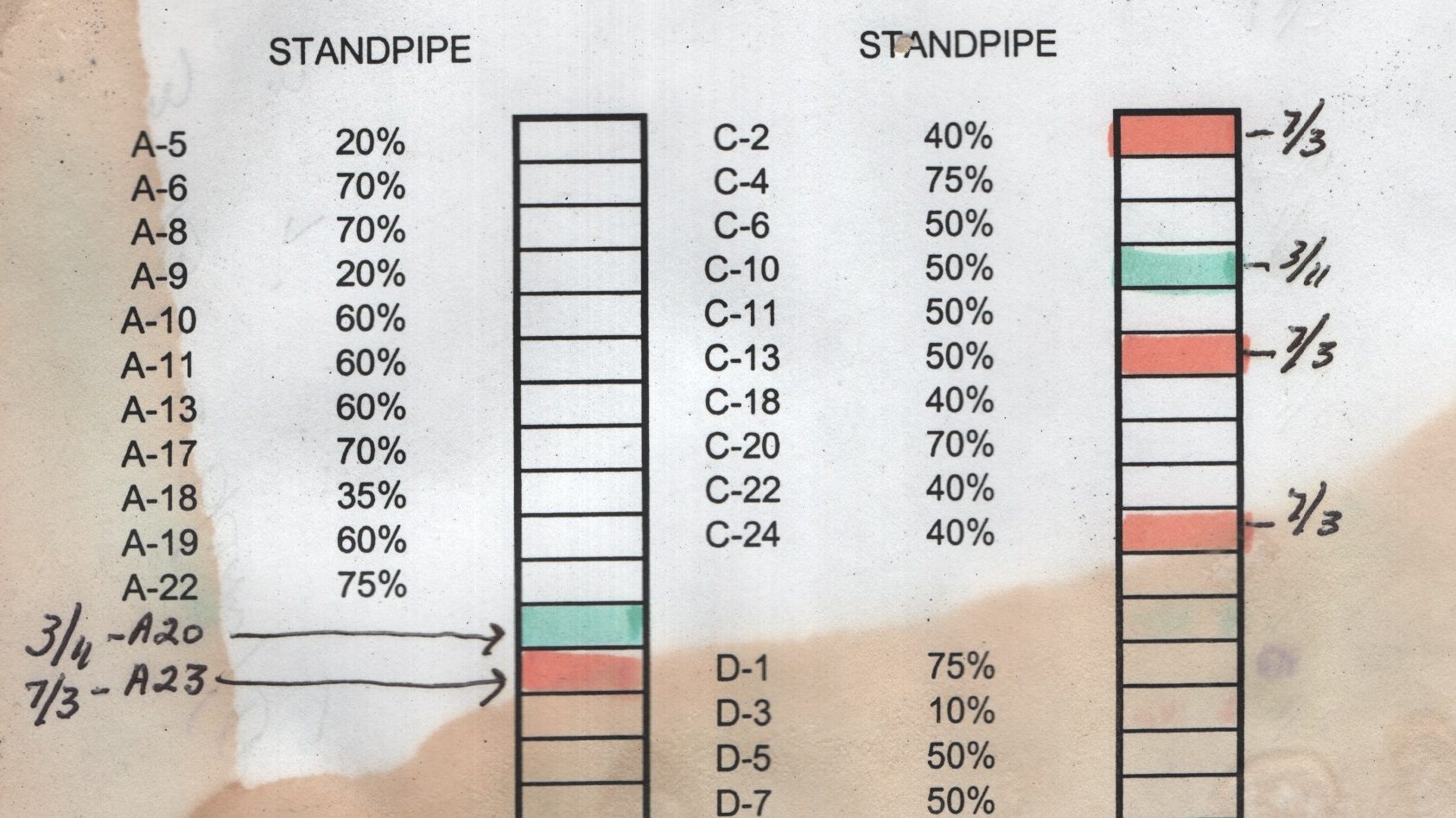
On the west side of the battery each oven had a refractory lined metal “stand pipe” with a cast metal “gooseneck” positioned on the standpipe. The gooseneck had a lid which after dampering an “oven off the main” was raised to inspect the standpipe and gooseneck for carbon accumulations which needed to be removed before recharging. At the back of the gooseneck was a water spray which filled a damper pan in the main to seal off the oven from the main. The goose neck was attached to a collector main which essentially accumulated the volatile gases driven off each oven by the coking process. Some tars in the gas also dropped out in the main and were drained every shift. The entire gas movement was facilitated by an exhauster (one electric, one steam backup) which was a huge gas pump sucking gas from the battery and pushing it thru the by products facilities to clean it and push it back to the batteries. This entire gas movement system had to be maintained without introducing air as much as possible. Otherwise the gas contained within the system would approach LEL (lower explosive limit) and the smallest spark would create a very disastrous situation.
When I am in the plant, I can’t help but try to imagine what the batteries looked like when they were functional, as so much is missing. Clearly anything that was steel was sent to the scrap yard.
Since quite a bit of the operation was “clean” scrap I would imagine that all of that was removed rather quickly. Coal storage tracks were being removed in the last few weeks of operation! Rails, stairways, pipework and machines gone were in an instant.
Hard to understand leaving the ovens filled with unfinished coke. Must have been a pretty abrupt shutdown to not wait the 18 hours to let the last batch finish.
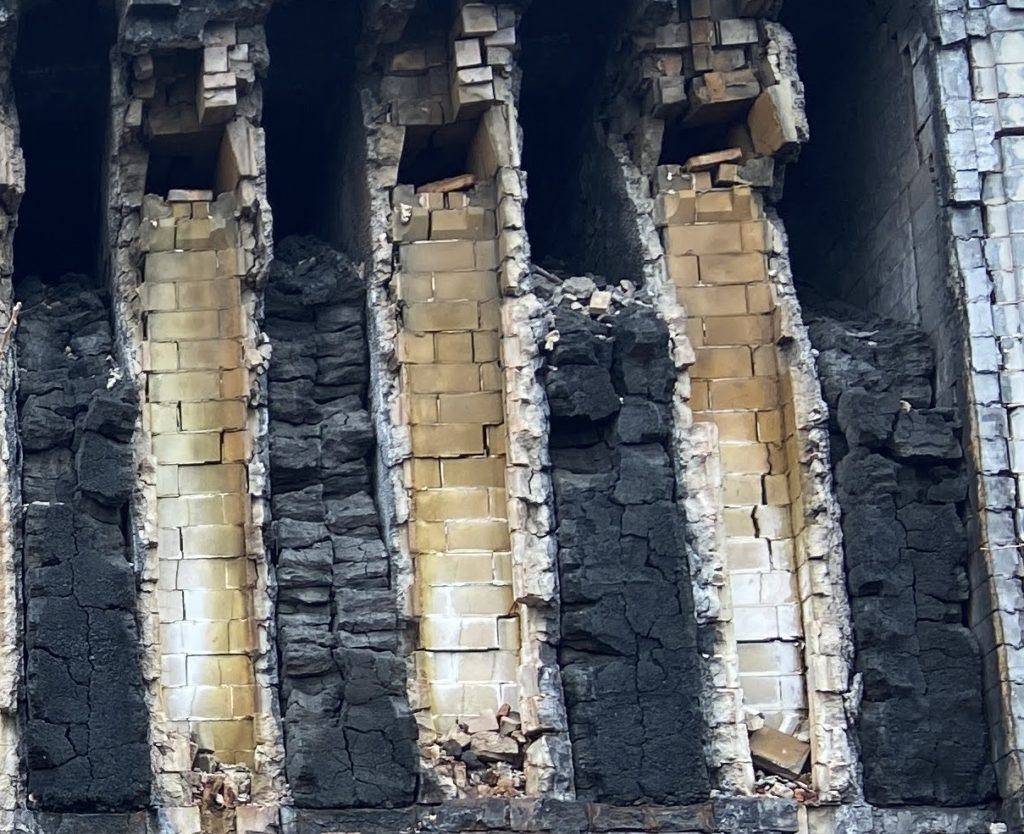
When I left for the last time couldn’t help but feel wastefulness but realistically coke was worth about $70/ton at the time and we were stocking quite a bit. We even were trying to produce foundry coke (a whole different animal) with marginal success. Our battery was only one of two left in the country with lots of productive life regarding blast furnace coke. Several years later when I was working for Indianapolis Gas converting their production from foundry coke to blast, I was told that ships arriving from China had cargo of marginal Chinese coke that customers were bidding on prior to arrival. Blast furnaces were bidding up to $500/ton for a marginal product…go figure.
5 replies on “Acme’s last oven manager”
This is great that you got in touch with him and was able to pick his brain and document it!
we actually met up, he gave me a killer acme steel mug which i have used many times, youve probably come across it already. we have sent hundreds of texts and emails and we still stay in touch. once we even did a facetime while i was in the plant! he gave me so many insights just so i understand more when im walking around.
Incredible 🔥
Doug, You have always been a class act. The last three years were rough on everybody, however, somehow we learned to survive. Some of the stories included touch a sentimental string with me. I think and dream about Acme and the people often. It was a great experience, despite of what happened. Thank you for doing this.
Doug’s contributions to this website are without question it’s greatest asset. We are blessed that I was able to contact him but also that he agreed to contribute. And in such a prolific way! His story’s importance in the historical content cannot be diminished. Thank you for commenting!