The third in a continuing series (Click the ‘Tales From Topside’ category heading above to see the rest). Doug Podgorny was area manager ovens up until the very end. With 25 years between the coke plant and mill, he watched things start to unravel but had to stick around to see it through. Never before has this story been told, first hand. Stick around for more.
Along with the purge plans we also had to develop a preservation plan. A majority of the assets needed to produce steel are such that with the right preparation they can be idled, even mothballed and then with the right touch be brought back online into productive capacity. That is, as long as there isn’t refractory brick in play. Once refractory brick has been at heat then cooled to ambient its structural integrity is a crap shoot and a coke oven is little more than a stack of refractory bricks. The odds of it being cooled to ambient and then fired back up successfully are about as great as hitting the lottery, but you can’t win if you don’t play.
I always looked at the plant itself as a living entity. The coke ovens themselves were the body with all the gas/air piping like arteries and veins. The coal handling department fed the beast with a steady diet of specially prepared coal. The by-products department processed the waste but also contained the heart: the exhauster that sucked the waste gas and pushed the clean gas back to the monster. The oven chambers themselves were essentially a living organism with carbon being the growth agent. As any good coke plant operator would tell you,”carbon can be your best friend or your worse enemy”. Just the right amount of carbon helps hold the silica brick where it needs to be, seals minute cracks in the walls and flues to stop emissions and even acts as a lubricant during the push. Too much carbon and hard pushes go up and stickers (ovens that won’t push out) increase, both of which increase damaging pressure on the oven wall. But if the whole thing cools to ambient you lose all the carbon as well. So more realistically, the odds of a good restart after shut down are really only half as good as the lottery. But we didn’t focus on that.

Monday morning at the plant started as usual, what had become the usual anyway. Discussions regarding our speculation and rumors of when “it” would happen. A lot of us at the plant still questioned the wisdom of Acme’s decision to build the continuous caster. Acme as the smallest integrated steel mill in the US long understood they could not compete with the much larger steel companies. Acme did however find its niche. We made over 400 different types of steel the big guys didn’t want to mess with. Acme’s existing facilities were tailor made to make smaller batches of specialized steel. They had bought several companies that needed these steels who became captive customers. Even in the leanest times Acme would almost always generate a profit.
Yes, the facilities direly needed a modernization. Yes, Acme borrowed 400 million to build the worlds then most powerful caster. We could now make steel and roll it directly from the metal produced at the blast furnace. No more billets to reheat then roll out. We could shutdown several operations, save a bunch of overhead and be the industries low cost producer. Or so it was touted by the new executive team. A major undertaking which would “change the culture” at Acme. And it sure did! Unfortunately the caster, (which is most profitable when large batches of same steel are run through it) didn’t seem to fit what had made Acme Steel a success! I personally had voiced that opinion several times at operational meetings. I was told I was failing to see the “big picture” ! Add the untimely (for Acme and the American steel industry) dumping of foreign steel which flooded an already depressed market and drove down the market price of steel. Acme was deep in debt, and in an increasing amount of trouble. This was further exacerbated by a very difficult learning curve and troublesome time working out the bugs in the “new” culture. Repaying the 400 mill was failing. Acme was bleeding losses, but not to worry – Bank of America borrowed us another 100 million!
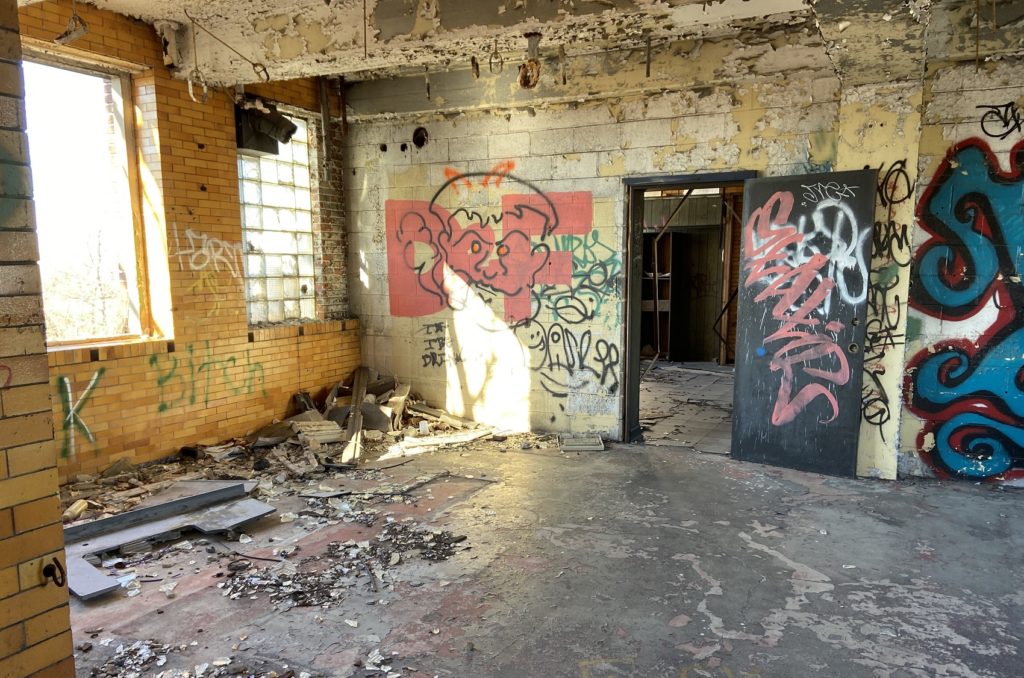
Soon the call came for an unscheduled meeting in the division managers conference room. Not good news – what else could it be? The shutdown was on. Knotted stomachs all around from that point on. It was a very short meeting and almost emotionless. Simply put: loans were due, BOA rejected borrowing additional funds and the coke plant would no longer have money to buy coal. Without coal of course the monster would soon wither and die. However, someone did mention that there had been some interest in potential buyers with the sense to know coke would one day be a money maker so we were all hoping to be bought out.
With that in mind we set about the business of preserving the battery. By far the one of the worst parts for me was gathering battery personnel together to inform them of our course of action. Thankfully no one freaked out. Everyone took it as well as could be expected. And I was sure to stress the possibility someone would buy us out from under the Acme disaster. We immediately put our plan into action. Most resources were already on hand. Coordinating and positioning were first. We targeted next Monday as the day of the purge. There was still a weeks supply of coal on the ground so we hoped someone would step forward soon! We continued to operate but at a reduced schedule.
We also decided to leave every oven full on the final day for several reasons. Being full of hot coke would allow the battery brickwork to cool at a much slower rate. The coke charge would also hopefully help support the brickwork. In theory this could give us 4-7 days before the ovens went beyond recovery. We would end the push/charge cycle Friday and as the ovens ended their coking cycle we would damper them off the main and let them “soak”. There would be plenty of gas to pressurize the main till Monday (November 18th 2001), leaning it out enough to remain above the LEL but the minimum amount wasted to the air. The days flew by. The nights dragged. Restless sleep with thoughts of unemployment . I’m sure I wasn’t alone!

When Friday arrived we pushed the last oven early, charged it up and began to seal the battery. We would let the coking process continue and be ready to purge sometime on Monday. I don’t remember exactly how long it took, time would alternately fly by then drag throughout the long day. I do remember making the call to let the front office know we were done. The next day for most of us was busy. Flooding the battery top with clay slurry, packing everything we could with Kaowool and everything else we planned to help retain the heat on the battery.
I decided not to clean out my office. I just knew somebody would buy the plant. I thanked everyone who stuck around personally, said my goodbyes and showered up to go home. The first shut down was completed successfully. Just a wish and a prayer but sometimes that’s all life gives you. It was a longer than usual drive home.

4 replies on “The Shut Down”
Amazing to read, brings back memories, I worked at this coke battery on a shut down cladding the 24″ main gas pipe under the battery. Also working at the rolling mill and BOF as an union pipefitter. Those were the days and some of my best and greatest memories pipefitting If this is read could you please respond as it would make my day so to speak.
Joe your comment has definitely been read! You made my day as well! I will email you tonight!
Union pipefitter working down the street at ozinga, reading up about this area. Pass Acme steel mill ruins daily.. saf
glad to hear there is still work on the SE side to be had for pipefitters. i recommend you duck into the plant one day when your shift is over! thanks very much for commenting!